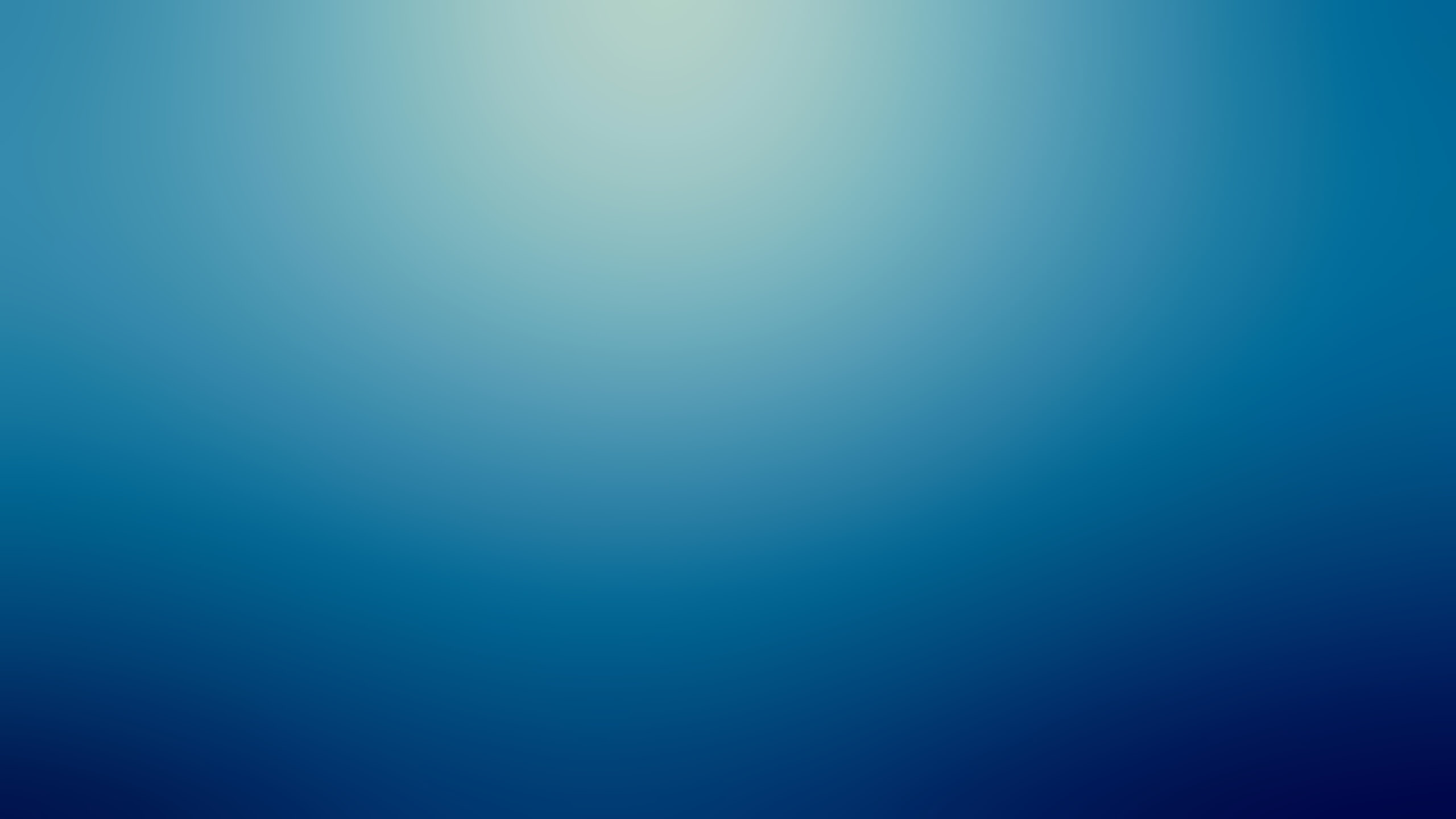
The seven deadly wastes of Lean
Over the past week, we tackled the Seven Deadly Wastes via our Social Media channels. For those of you who missed it, we have reposted them all below.
Please feel free to share where you have observed these wastes in organisations you have worked - we'd love to hear from you!
#1. The Waste of Overproduction
Producing things because we can, rather than only producing enough to meet customer demand.
.png)
#2. The Waste of Waiting
Waiting for information, goods, or decisions to be made, causes work to stop and cycles to be lost forever.
.png)
#3. The Waste of Transport
Moving goods or people without reason or purpose provides no value to the customer.
.png)
#4. The Waste of Overprocessing
Doing more than the customer wants and is prepared to pay for creates no value for the customer or the company.
.png)
#5. The Waste of Inventory
Building too much inventory ties up capital and risks the goods expiring or becoming obsolete.
.png)
#6. The Waste of Motion
Any movement that doesn't add value to the product is waste - consider how you can reduce unnecessary motion in your work.
.png)
#7. The Waste of Defects
Build quality in, rather than test for quality at the end. Defects create costly rework and remediation.
.png)
Download